High Job Satisfaction Keeps Turnover Rate Low
White Rock Is Among Industry Leaders In Employee Retention
(May 2001)
“Everything!”
Thats what employees of White Rock Quarries say they like best about working for the company.
When pressed for more details, a number of factors come up to explain how the company maintains a turnover rate less than half the industry average. The bottom line is, people who come to White Rock tend to stay at White Rock.
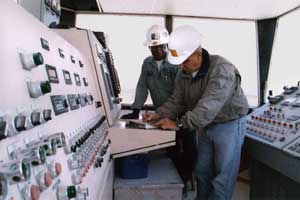
In the aggregate plant control room, Day Shift Plant Operator Arturo Pelaez enters the latest production figures, as Pit Foreman Nate Malone looks over the log sheet. Pelaez has been with White Rock since the plant opened in 1988.
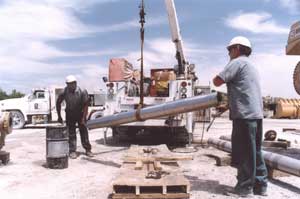
Elijah Holmes, left, a White Rock employee since 1990, helps Mechanic Charles Payne, Sr. prepare a new pivot shaft for installation in a Cat-8 dozer.
“Its much different here, much better than other places,” says Fidel Almeda, through one of his bi-lingual coworkers at the heavily Hispanic, northwest Miami work site. An off-road haul truck driver, Almeda has worked at White Rock since 1988 when the product line was expanded to include processed aggregates. “Im happy with the people I work with and the supervisors.”
The benefits package is another reason workers are satisfied, especially the 401(k). And they like the steady work, with overtime. Workers at White Rock average from five to 15 hours of overtime per week, at time-and-a-half pay.
“They also make sure the equipment is taken care of,” says Ruben Washington, a Loader Operator hired in 1989. “Thats important.”
Mechanic Charles Payne, Sr., a 12-year veteran of the company, agrees. “That means a lot, having good equipment to work on. And the operators take good care of their equipment.”
Pit Foreman Nate Malone, who transferred from Ranger in 1986 to help start the quarry, explains that well-maintained equipment not only keeps employees happy, it increases White Rocks production.
“Maintenance makes production. If you dont do maintenance, you cant make good production. Youre going to have problems that catch you by surprise.”
Maintenance also makes the work place safer, something White Rock takes very seriously. For example, the aggregate plant schedules eight hours of maintenance for every 16 hours of production. The result is an efficient work place that hasnt had a lost-time injury in more than three years.
Even off the premises the company looks for ways to keep up morale, such as with an annual picnic for workers and their families, where thousands of dollars of door prizes are given away.
When you put it all together, what you get is a high level of employee satisfaction and as a result, a very low turnover rate.
“We treat everyone as we want to be treated,” explains Raymond Maddy, Vice President of Operations. “Most of our supervisors came up through the labor ranks, including myself, so we try to lead by example.”
WRQs Raymond Maddy Promoted To V.P. of Operations
(May 2001)
When it all first started, way back in 1986, Raymond Maddy was there, putting in the long days, building from the ground up a full-production limestone quarry in the competitive mining industry in northwest Dade County.
His title was Supervisor then, but over the years his career continued to progress. He eventually became the companys Operations Manager but even that was still just a stepping stone.
In April, Raymond was promoted to Vice President of Operations, a fitting reward for his many years of excellent service as the quarry has grown to one of the top 10 producers in the country.
But dont expect the new title to change him. Raymond still wears the same uniform as everyone else and still spends most of his days out in the pit overseeing the operations as he has done for years.
“Raymond is one of the true cornerstones of White Rocks success,” notes WRQ Executive Vice Pres. Jim Hurley.